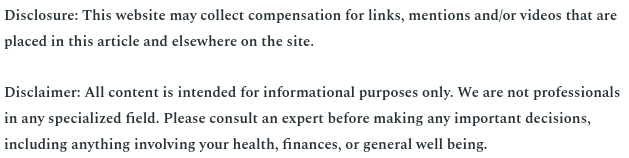

Without realizing it, you’ve most likely seen countless products that are formed by the custom plastic rotational molding process. Rotational molding, sometimes shortened to rotomolding, is actually a fairly simple process to understand. It’s responsible for making everything from plastic rolling laundry carts to plastic lockers. Essentially, it’s the ideal process for making plastic, hollow objects of almost any shape or size. But just how are these objects made? Here’s a closer look at how custom plastic rotational molding is accomplished:
- Preparation
First, a hollow mold is filled with polymer powder (often polyethylene) or resin. The powder or resin can be designed to make a specific color during this stage. The mold is then closed up, locked, and put into a pre-heated oven. The oven temperature will be somewhere between 500-700 degrees Fahrenheit. - Heating
While inside the oven, the mold is rotated around two axes so that the polymer powder or resin can melt and coat the entire interior. It’s a slow rotational process, but timing is of the utmost importance. The success of the final product depends on the exact amount of time the mold spends in the oven. If it’s in for too long, the polymer will degrade; if it’s not in long enough, the process will be incomplete and bubbles will form in the product. - Cooling and Removal
Once the correct timing has been achieved, the mold is removed from the oven to cool. The method of cooling can vary. Sometimes it’s done by fan, other times by water. The cooling step will solidify and slightly shrink the product so that it can be removed from its mold. This step also has to be timed carefully, as rapid cooling can warp the product. Once it’s cooled down and is solid enough to keep its shape, the mold is opened and the product is removed. Then, the process can start all over again.
Unlike other plastic molding processes, custom plastic rotational molding doesn’t require any additional pressure — just intense heat. Although it takes an expert to get the timing and specifics down to a science, it offers a cost-effective and design-friendly way to create products we use on a daily basis.